Why is Precast Technology Becoming More Popular in the Indian Real Estate Development Sector?
- 19th Feb 2023
- 1542
- 0
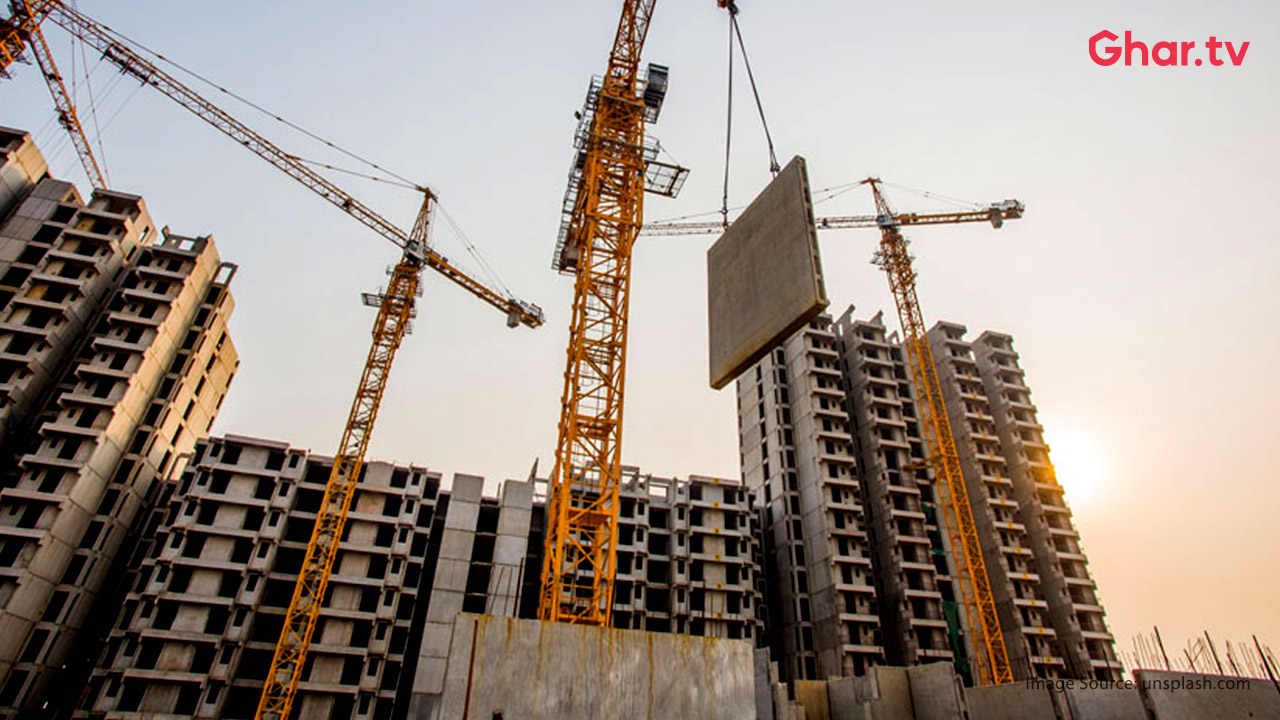
Never miss any update
Join our WhatsApp Channel
Precast Technology in The Indian Real Estate Development Sector
With the efflux of time various technologies pertaining to multiple sectors have evolved. This includes the real estate construction industry too.
The Growth of Precast Technology
With the real estate construction sector embracing new technologies, precast technology, has lately won favour with developers and real estate is one of the industries where precast technology is getting the most traction.
Several components or pieces of a fundamental construction structure, such as slabs, roofs, beams, wall panels, columns, support wings, etc., are custom designed and built away from the construction site in a quality-controlled factory, and then combined on the final construction site.
These are some of the benefits and drawbacks of precast technology:
Some of the most important elements that make precast technology advantageous for the real estate building industry are as follows:
While the pieces are manufactured in a factory under a controlled environment, many tasks, such as manufacturing the parts, concrete casting, and finishing, may be performed concurrently, unlike the manual process, which takes several days to fix simply the cement and bricks.
In addition, since everything is produced to order, the plan for each element's form, size, and weight is defined, saving a great deal of time. It has been discovered that this technique reduces the time required to construct a building by at least 50 percent compared to conventional approaches.
The use of this technology removes the possibility of human mistake since the separate structures are manufactured by machines. In addition, the most essential parameters that impact the quality of construction - construction, casting and curing, temperature, design-mix, and frameworks - may be monitored in minute detail.
Due to the fact that these individual components are evaluated against all conceivable effects that might be generated by natural processes such as corrosion, acid assaults, and precipitation (water seepages), they are more durable than those manufactured using conventional techniques.
Even though a substantial initial investment is required, the financial rewards upon the completion of the construction are substantial. Reason: There are no or minimum maintenance costs.
Also, enhanced longevity prevents costly repairs and restorations. In addition, since the framework is finished in roughly half the time required by conventional techniques, the developers may complete their projects more quickly and go on to the next one.
Many issues associated with precast technology are described below:
Narrow highways and a large number of flyovers/skywalks/metro lines make it harder to move these massive components from the manufacturing facility to the building site.
Damage control: We lack the availability of a damage control system in the event that components are damaged during transport, since regularly recreating these pieces would not serve the fundamental aim (time management and cost-effectiveness) of using this technology.
While the buildings are custom-made, there is little flexibility for adjustments, which is a significant negative that might significantly impact the end product.
India has a very variable environment and is subject to several natural disasters, making it difficult to test the buildings.In order to increase the performance and relevance of technology, it must be modified in accordance with the climate, terrain, and soil of the place.
Several specialists in the Indian real estate building business suggest that big real estate companies should progressively use precast technology since it reduces construction time by around 64%. According to building construction experts, developers should investigate new building materials, such as self-healing concrete, aerogels, and nanomaterials, as well as innovative construction approaches, such as 3D printing and preassembled modules, because they can reduce costs, accelerate construction, and improve quality and safety.
Comments
No comments yet.
Add Your Comment
Thank you, for commenting !!
Your comment is under moderation...
Keep reading blogs